Wax Injection
Investment casting
By the lost wax process
The lost wax process allows us to manufacture highly complex parts by delivering a variety of configuration details and specific surface finishes while complying to stringent tolerances. Easily modified tooling and the inherent versatility of precision investment casting minimizes operating costs.
At Alphacasting, we have perfected a lost wax casting process, thus enhancing the manufacturing of thin-walled parts with high structural integrity.
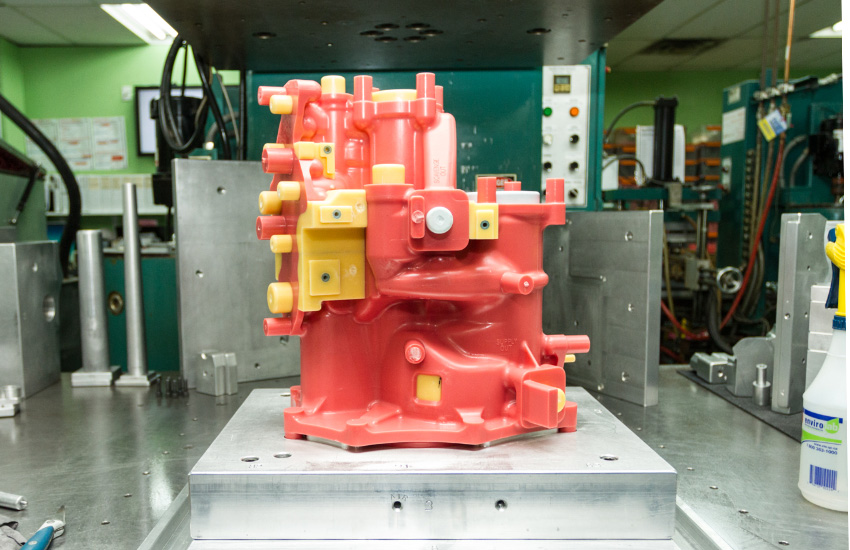
Precision
Performance
Flexibility
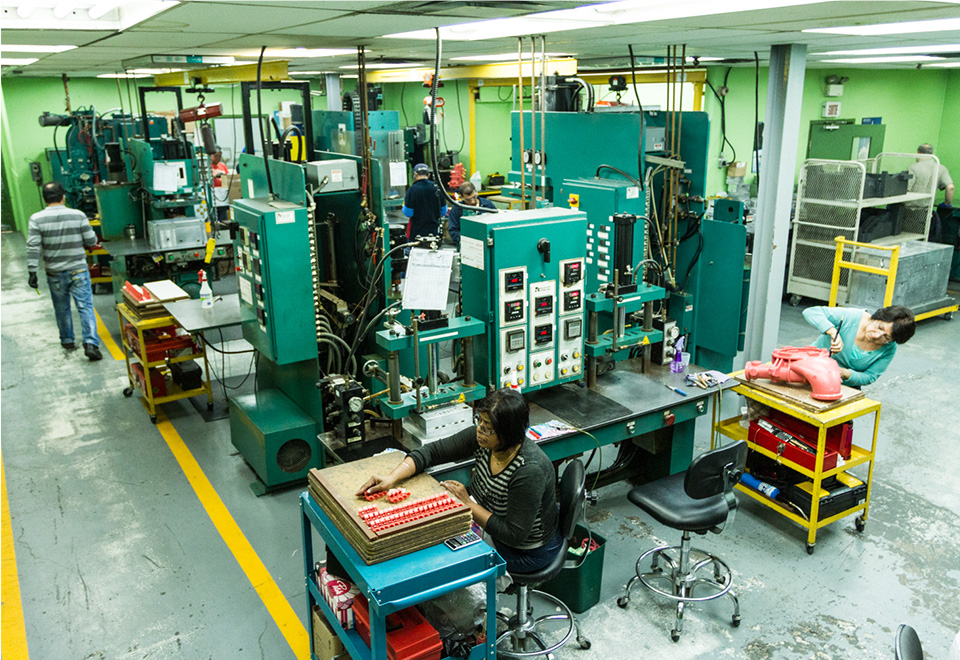
Alphacasting is a unique foundry:
we cast different alloys with the same tooling because we maintain tight tolerances, and we have dedicated lines for steel, aluminum, and titanium alloy castings. Our high-volume small presses reach 100T capacity for large structural tools. Our automated mould production lines for large structural parts increase the capacity and reliability of mould performance.
The process
Once the design phase is completed, the mould is milled or spark-eroded and assembled by a specialised toolmaker. Alphacasting is responsible for the design and development so that the mould can be produced externally using the most advanced processing machines.
The lost wax process includes pouring of molten metal into the mould that has been created by means of a wax model. This wax model is melted and drained away once the mould is made.
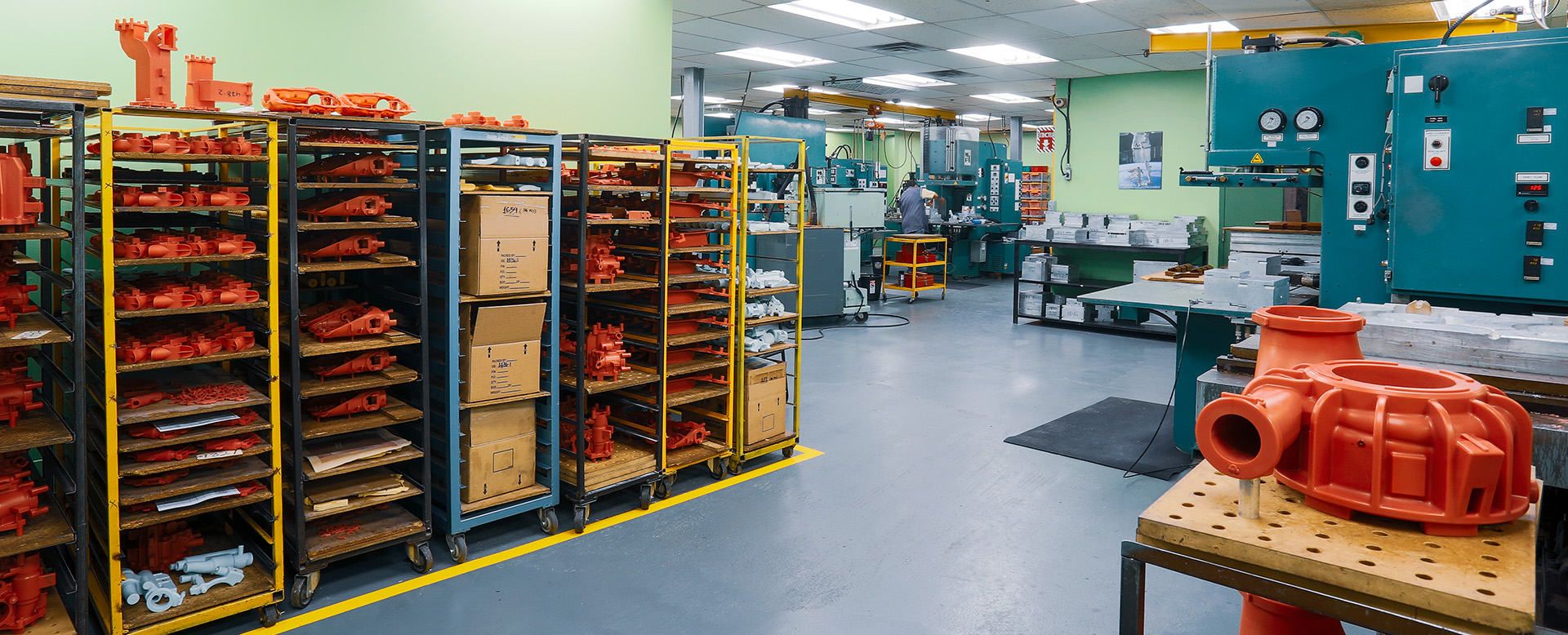
General features of wax injection moulds
- Suitable for both small series and large series of castings
- Nearly unlimited lifespan
- Single investment for nearly infinite production capacity
- Wax injection moulds are made of aluminium or steel
- Extremely high dimensional accuracy
- No draft angle required because the wax model shrinks
- Provided with cores and slides to meet design
- Good heat transfer
- Wax model identical to final cast piece
Manually operated versus automatically operated moulds
There are two types of mould processes: a manually operated and an automatically operated matrix.
A manually operated mould is operated manually on a wax injection press by an employee. However, the wax injection cycle itself runs completely automatically: processing times and injection pressures are controlled by the wax press. A manual process provides a favourable price level mould, is suitable for both small series and medium-size series of castings and is fabricated from either aluminium or steel. The mould can contain multiple cores or slides.
When using an automatically controlled mould, the wax injection cycle and mould operation is electronically controlled by the wax injection press. The production of large series of wax models runs entirely standalone (without personnel). Moulds are often very complex in terms of design and dimensions and often contain complex electronics, hydraulic and pneumatic systems. The automatic application is suitable for large series of castings and/or long-duration projects, as it is always made of hardened steel, implying an unlimited lifespan.
Extremely high dimensional accuracy = ALPHACASTING Solution