Moulding
A world-class facility & competent workforce
AT EVERY LEVEL
Our modern 74,000-sq-ft facility is located in Montreal. It is 40% temperature controlled and features state-of-the-art equipment:
- Fully automated wax injectors
- Robotized molding room
- Programmable burn-out furnaces
- Image analysis system
- Coordinate-measuring machine
- Aluminum heat-treating furnace
- Tight control of all processes
This equipment is handled by our skilled employees and an engineering team on hand at the plant. Together, we apply our high-quality standards to meet your most complex requirements for your casting projects.
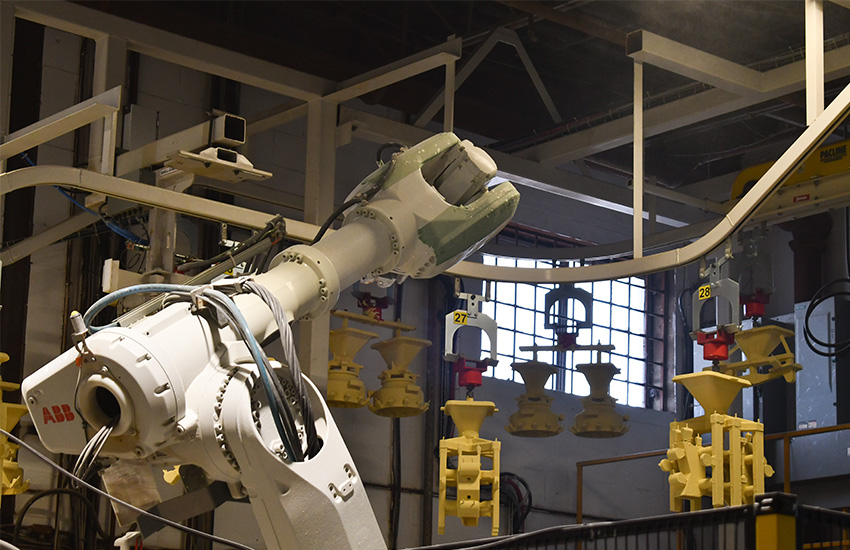
Wax Pattern
and Mold Shell
Wax patterns are created to make the process of parts creation more economical.
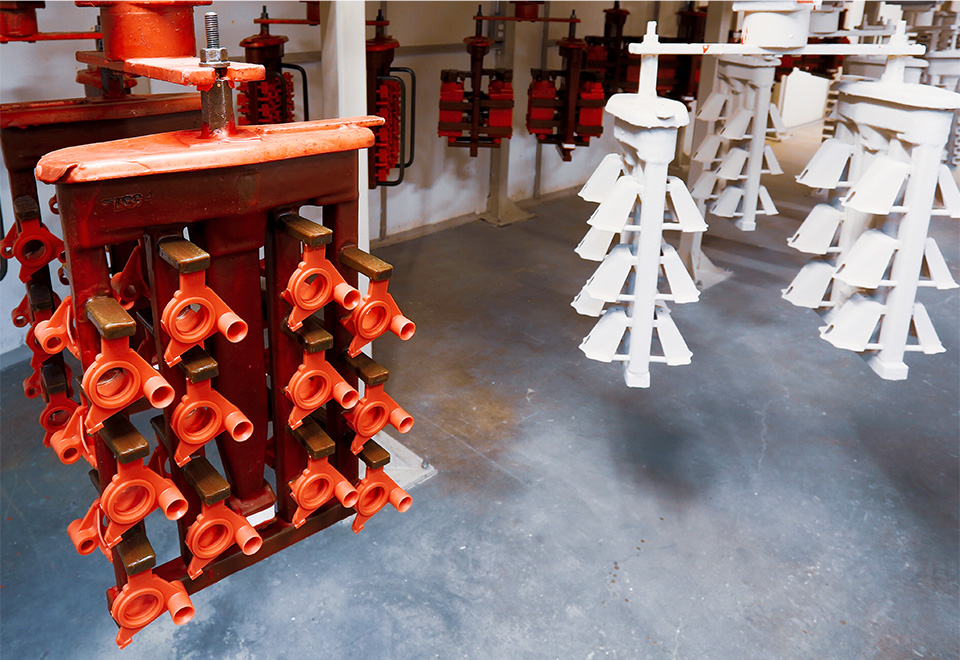
The wax patterns are attached to a wax “sprue”. The sprue serves two purposes:
- A mounting surface to assemble multiple patterns into a single mold, which will be later filled with alloy.
- A flow path for the molten alloy into the void generated by the wax pattern(s).
The wax between the pattern(s) and the sprue are called “Gates”, because they control the flow and direction of the alloy into the void created by the pattern.
The next step in the procedure is to make a ceramic shell around the wax tree. This shell will eventually turn into the mold in which metal is poured. To form the shell, the tree is plunged into a ceramic bath or “slurry”. A six-axis dipping robot assures consistency and uniformity of shell production in intricate and complex parts. After dipping, fine sand or “stucco” is spread to the wet surface.
The mold is left to dry, and the process is repeated until a layered (or laminated) ceramic mold, capable of withstanding the stresses of the casting process, has been made. The desired thickness of the mold depends on product size and configuration exigencies. Once the last coat of the ceramic shell is completely dried, it’s ready to handle molten metal during the casting process.
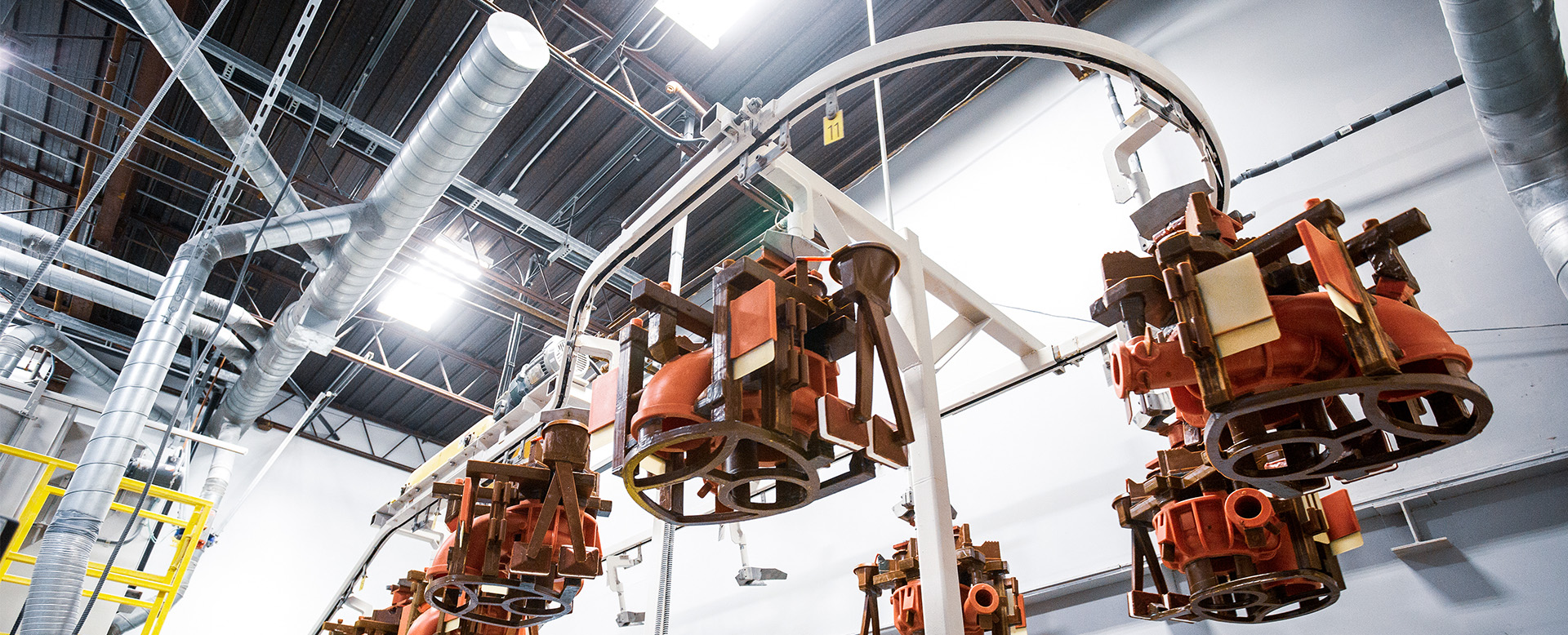
Skilled employees & Engineering team = ALPHACASTING Solution