Titanium
Titanium
An ideal metal
Titanium is in a class of its own. It is known for its purity, low density, light weight, high strength, non-magnetic properties, and excellent corrosion resistance. In short, it’s the ideal metal. It has a relatively high melting point of 3000oF (1650oC) making it a useful material for elevated temperature applications. Titanium is often used in the industrial market for applications requiring state-of-the-art technology.
Alphacasting pays close attention to details when designing complex tooling configurations for all types of alloy parts to suit specific customer requirements. We have perfected a lost wax casting process that allows the manufacturing of thin-wall titanium parts with high structural integrity.
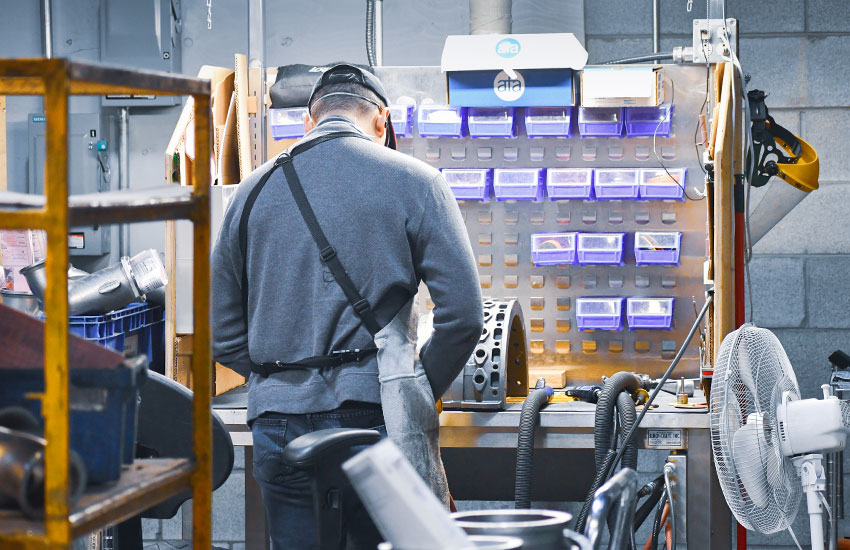
Titanium’s main
Characteristics
Titanium alloy components are increasingly popular and affordable, and exhibit unique properties which are sought after by many industries:
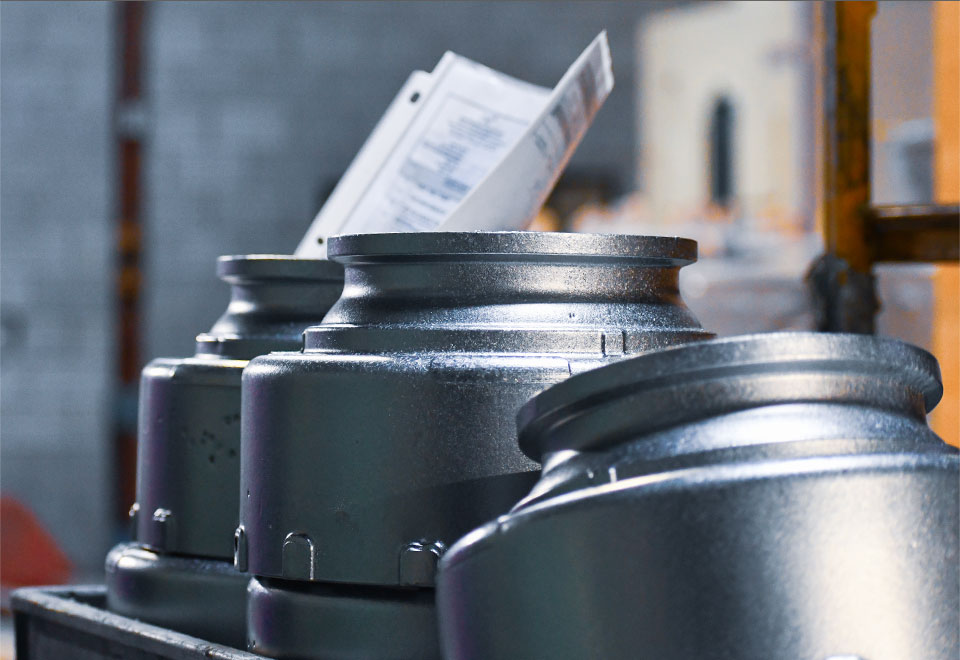
- Low density
- High mechanical strength
- Good fatigue resistance
- Excellent resistance to oxidation
- Low coefficient of thermal heat transfer
Investment Casting of
Titanium Alloys
Investment casting uses a shell system to help control the surface finish and detailing of the casting. This proven casting method is the only process that can produce complicated shapes in high temperature alloys to a very high-quality standard.
The shell system and the shell technology, including the control, maintenance, composition and operation, have the biggest effect on the quality of the casting. The shell system comprises a face coat system and a back-up system to produce the shell mould. Apart from the quality of the wax pattern, the composition of the slurry and the stuccos used for the shell manufacture as well as the physical properties of the slurries, control the surface finish of the casting and the definition of the features of the casting.
A wide range of titanium cast alloys exist, and titanium castings are successfully being implemented as cost-effective alternatives to forged and wrought products for high performance and increasingly cost-sensitive applications such as military and commercial aircraft airframe structures.
For most of the last two decades, investment casting has been the preferred processing route for sophisticated titanium castings.
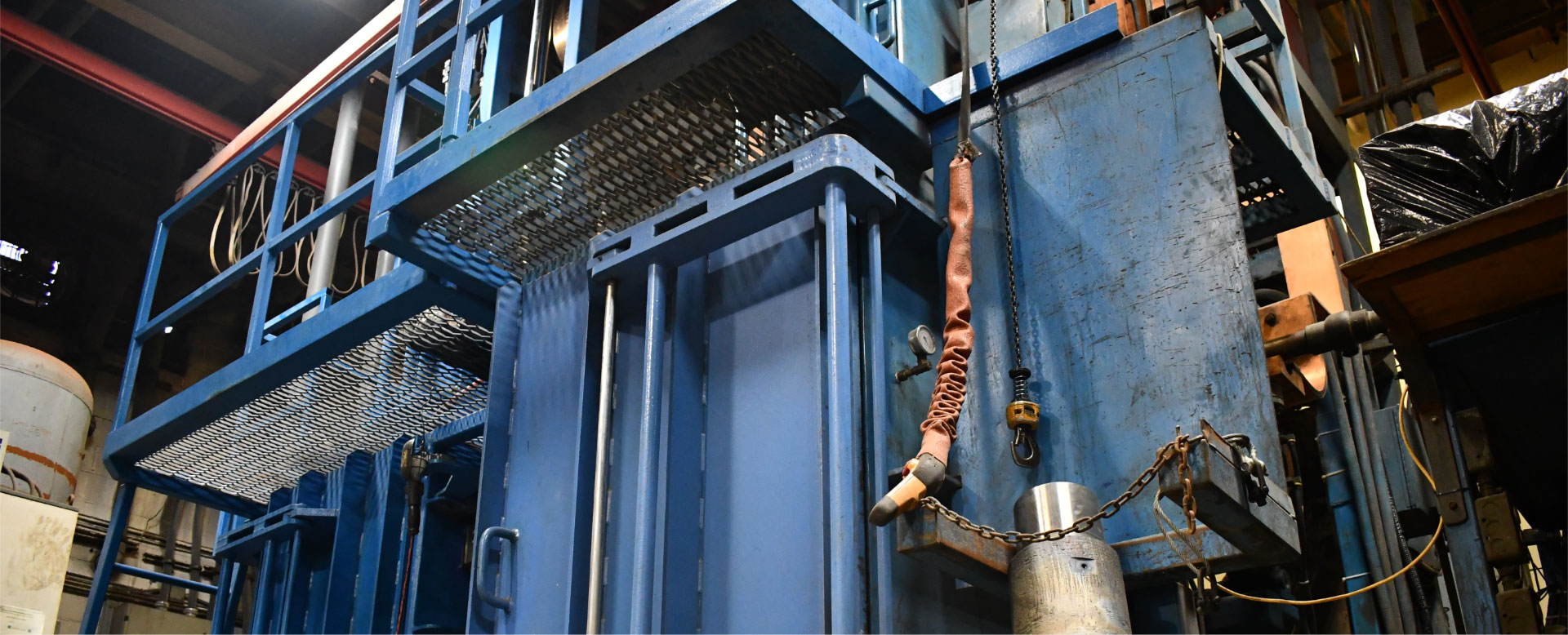
The most widely used titanium alloy nowadays is Ti-6Al-4V
This alloy possesses an excellent combination of strength and good corrosion resistance. Common applications include aerospace, surgical implants, pressure vessels, aircraft compressor blades and discs, etc.
Aluminum stabilizes the hexagonal close-packed (hcp) α phase, and vanadium, being body-centered cubic (bcc), stabilizes the β phase. Melting and pouring of titanium alloys must be performed under vacuum because of their high melting point and excessive reactivity of the melt with crucibles.
The use of net-shape or near-net-shape technologies are garnering interest considering the large cost saving potential of this technology in manufacturing parts of complex shapes. Precision (investment) casting is by far the most fully developed net-shape technology compared to powder metallurgy, superplastic forming and precision forging.
An increase in production of precision castings of titanium alloys was noted recently. This may be attributed to its significant cost savings compared with the complicated process of machining. For many alloys, mechanical properties of castings are inherently lower than those of wrought alloys. Nevertheless, heat treatment of titanium castings yields mechanical properties comparable and often superior to those of wrought products.
Chemical milling process
Chemical milling consists of using baths of temperature-regulated etching chemicals to remove material to etch, cut or engrave specific designs or patterns in the material and create an object with the desired shape. This process is performed after the casting parts are manufactured. It is characterised as a subtractive manufacturing process.
It is mostly used on metals, though other materials are increasingly important. It was developed from armor-decorating and printing etching processes developed during the Renaissance as alternatives to engraving on metal.
The process involves bathing the cutting areas in a corrosive chemical known as an etchant, which reacts with the material in the area to be cut and causes the solid material to be dissolved; inert substances known as maskants are used to protect specific areas of the material as resists.
State-of-the-art technology = ALPHACASTING Solution